BLOGS
NEWS & UPDATES
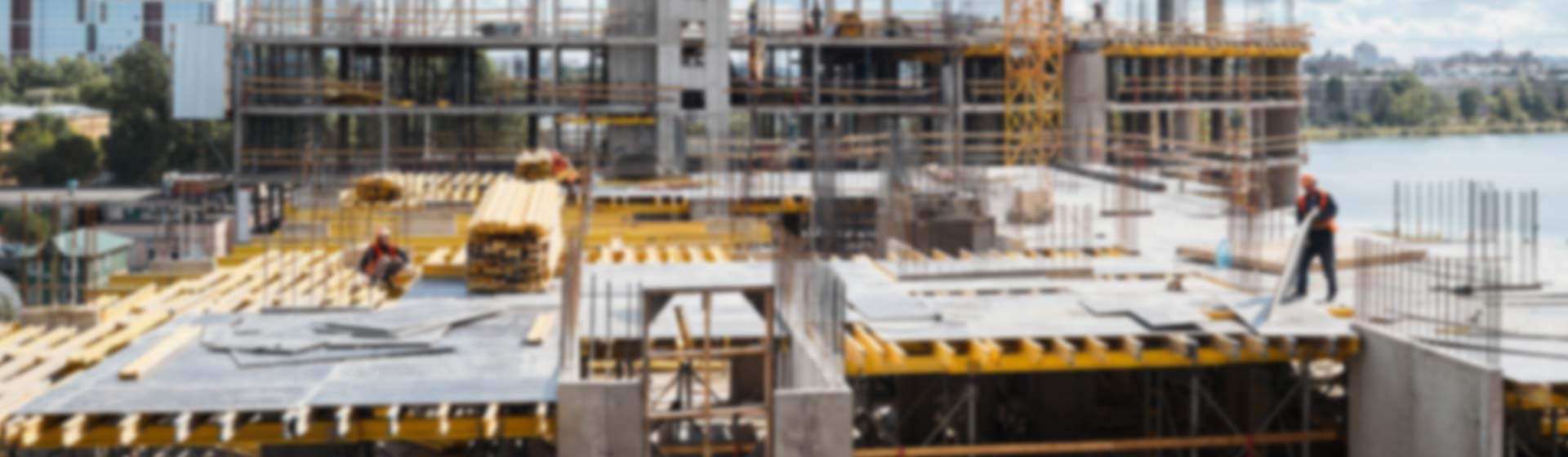
Construction projects come in all different sizes, from residential buildings to massive factories and distribution centers covering hundreds of acres. Each of these projects have one very important aspect, the potential for serious injury to workers. Nobody wants to see members of their crew get hurt on the job, but in the thick of arduous work, employees focused on completing a task can become complacent to some of the hazards they create in the normal process of their work. These mistakes can not only cause injuries to themselves or other workers but may result in expensive fines for a business. The best ways to prevent injuries will always be instilling a culture of safety within your company and to ensure workers are properly trained in safe work practices, but even the best-intentioned make mistakes while focused on getting the job done. So what other tools are available to construction businesses to keep these mistakes from turning into costly injuries and fines? Site Safety Audits Large construction sites with dozens or even hundreds of workers will require on-site safety professionals to constantly monitor hazardous conditions and ensure hazards are quickly identified and corrected. However, for smaller sites like a new build or renovation of apartment complexes, this may not be a practical approach. For these projects it may be more beneficial to have trained safety professionals provide site safety audits on a recurring schedule. Site safety audits are walk through inspections of your projects by trained safety professionals who specialize in identifying the hazards common to construction sites. During an audit the inspector will thoroughly inspect all the areas of the project and look for any manner of hazardous condition, such as slip/trip/fall hazards, electrical hazards, fire hazards, and more. Once the inspection is complete, the company will receive detailed reports on what hazards were identified, providing them with a clear path forward to improve the safety on their worksite. But….Why??? Site safety audits seem like simple tasks to complete, so why shouldn’t companies just designate one of their current workers to simply do a walkthrough of the site themselves? There are many reasons why hiring third-party site safety inspectors versus having workers from the project complete these tasks, here are 5. 1. Unbiased Inspectors. A new person coming to the site will provide “fresh eyes” to the conditions of the worksite. Workers on a project may become simply numb to their surroundings because they are looking at them all day, every day. They may overlook things like simple trip hazards that they have become accustomed to stepping over throughout the day. 2. Training & Experience. Safety professionals are trained in not only safe work practices, but to OSHA standards, and they come with the experience to understand what is, and isn’t, acceptable on construction sites. Through this experience your auditor can ensure that things like flammable materials are stored properly, fall protection measures are adequate, and signage appropriately identifies hazards per OSHA regulations. 3. Attention to Detail. The workers completing the project are already inundated with tasks and duties to support the completion of the project and adding additional tasks to them will either take away from their current duties or add extra time to their workdays. Walking through sites requires taking the time to inspect the site thoroughly and complete a report of things to be fixed once the inspection is over. Site safety auditors have one task, which allows them to focus on that task. 4. Worker Morale. Bringing in a third-party safety auditor speaks volumes to your employees. Workers will see that your company is more concerned about ensuring they have a safe work environment than simply profit. Improving worker morale will foster the safety culture that is truly necessary for injury prevention. 5. Learning. Once your company receives your report, not only can you fix the problems identified, you can also teach your workers to be more aware of them in the future. The idea of the site safety audit is not to place blame on workers, it is to increase awareness of hazards and prevent them from reoccurring. Summary Site safety audits can be an extremely valuable tool on your construction projects to improve safety culture, identify hazardous environments, and prevent costly injuries or fines. Proficient Training & Consulting’s Safety Professionals always consider worker safety to be the most important aspect of their duties and strive to end avoidable workplace injuries. Our number 1 priority is, and always will be, ensuring all of your workers go home in one piece at the end of each shift. Contact us today to receive more information about how we can help you and receive a quote for this, and all of our other important safety services.
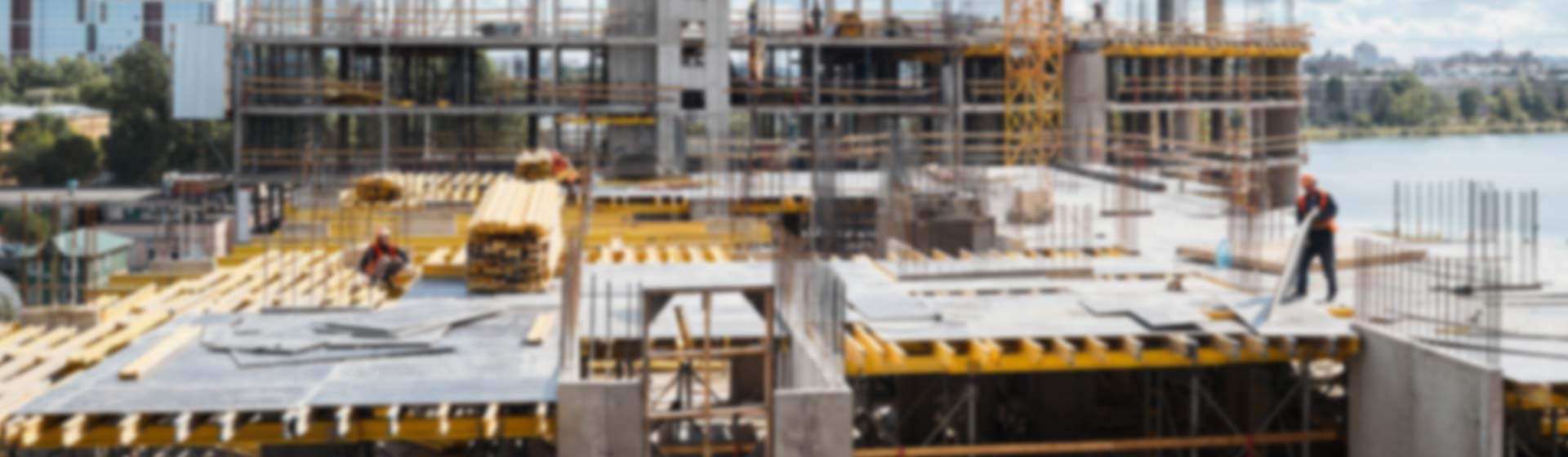
We’ve all heard it from the older trades’ workers on our construction projects, the statement “I’ve been doing it this way for 30 years and I’m not changing it now.” It’s often said when new equipment or procedures are handed down from management that allows for safer work, or in regards to new regulations from OSHA. Usually, those words are followed by another equally dismissive “When I started in this industry, we didn’t have safety (professionals) on sites.” When someone says that they aren’t wrong, however, what they ignore is the amount of people, some of whom were their friends, were seriously injured or killed while working on jobsites before and in the early years of OSHA. In OSHA’s early years, 1970 – 1975, the rate of non-fatal recordable injuries/illnesses to full time workers reached 11.0 per 100 full time workers each year! To put that in perspective, in 2018, that number was 2.8! There are a variety of reasons for this change, increased regulation, technological advancement, the 1980 U.S. Supreme Court ruling affirming the rights of workers to refuse unsafe work and to know the hazards of their worksites, among many, many others. So why do workers put up such a fight when we as safety professionals and supervisors are trying to implement change that makes their job safer? Why is there such a resistance to positive change? Many of those who are resistant to change are now running projects and supervising workers, as they should be as highly experienced workers, but they view the risks that were considered acceptable when they were apprentices or young journeymen as acceptable in order to complete the job on time and under budget. They then use this mindset and create a culture within their companies that since they accepted those risks, only a lesser worker would deny those same risks. This perpetuates a culture that the acceptance of unnecessary risk is a necessary evil on the job, and to challenge this, is a direct attack on the lifetime of work they have completed. Psychologically they can’t help but think that since someone is showing them a new way to do something, that they must have been doing it wrong their whole career, and nobody likes to hear they are wrong. However, the point of change isn’t telling them they are, or have been, wrong. The real point is to continually try and do better, be safer, have higher profit margins, and use less resources in the completion of the work we do. Does the U.S. Army line up in battle such as was done in the Revolutionary War, or do we utilize the tools at our disposal and send in guided missiles, or use armored vehicles? Of course, the military uses technology to complete its’ mission, because the greatest resource we have are our people, and we must protect them, much like in construction. So how can we combat this resistance to change in our companies? The answer to this question is simple, but the implementation of it is quite the opposite; we must flip the culture from a resistance to change and acceptance of risk, to acceptance of change and resistance to risk. FROM THE TOP A culture of change can only come from one direction, the top to the bottom. As business leaders, supervisors, and safety professionals, we must be the first to understand why culture change is necessary, and what positive impacts it brings for us and our workers. The thing that most people will recognize immediately, money. Per the National Safety Council, workplace injuries account for BILLIONS of Dollars in direct costs annually, $1.3 million per death, and $44,000 per medically consulted injury. None of this even includes the indirect costs of any fines from OSHA, increase in workers compensation premiums, lawyers, time spent by administrative staff, or the hiring of new workers or paying overtime to pick up the lost time from work stoppage. None of this even accounts for the devastation to the company reputation, keeping customers from hiring you again, or workers willing to work for you. By far the most important impact is that workers will be exposed to less risk and go home at the end of their shift, instead of to the clinic or worse. EVALUATE AND PLAN After understanding why, the next aspect is to assess what changes may be necessary within your company to ensure you exude a safety culture and develop a plan for how to move forward. Start asking questions and looking into safety metrics to paint a true picture of what your current safety atmosphere is and where you want it to be in the future. For example, evaluate the time your employees spend on training and the requirements you have for them to possess. Assess daily aspects of your jobs, such as toolbox talks, prework planning meetings, and daily safety paperwork. Pull injury records and identify what injuries are most prevalent within your workplace and investigate what changes may need to be made to eliminate them, buying new equipment, increased training, hiring more qualified workers, etc. Part of the planning is also to create a clear and easy to use risk management tool to guide safe work evaluation procedures. Remember, the whole idea of this change is to become acceptant of necessary change, and resistant to unnecessary risk. IMPLEMENTATION Using all of the compiled information, move forward and implement your plan. This is truly where the rubber meets the road, and following a well-developed plan will decrease the resistance from workers. All of the managers, supervisors, foremen, etc. within the company must be fully on board with the plan. Any break in this chain will weaken the message that reaches the workers. To best achieve this, communicate a clear message to everyone on your team about what the changes are, what data has been used, and most importantly why the changes are necessary. Many workers see safety as only a catch word that supervisors use to appease the masses, and from talking to many of them, they do not truly believe that leaders or safety professionals TRULY care about safety, but really only care about profit. This is due to faltering compliance in regards to how safety standards are enforced, complaints are accepted, and training is done. Displaying this myth with your workers takes more than handing out company shirts with the words “safety first” on them. It takes dedication and time spent on the ground speaking with your employees, genuine responses to their concerns, and clear responses to those concerns. THINNING THE HERD Unfortunately, sometimes there are individuals on a team that simply refuse to change their ways and continue to resist the change. Therefore, part of the planning process needs to include steps to weed out those individuals who refuse to meet the standard set by leaders. Remember, sometimes branches need to be trimmed to ensure the health of the tree. SUMMARY The construction business, like many others, is continually evolving from the lessons of the past and present. No longer are the days of walking along iron beams 75 stories above ground without fall protection, or jerry-rigging tools. In the modern day, the most important thing is not how far in the green a business is, but rather how can it manage to ensure its’ workers return home unscathed after every shift.